OVMS
Online Bottle Dimensional Measurement System

Simple
Can be setup and maintained by trained plant personnel.
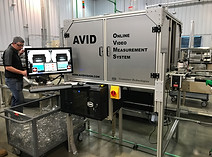

Versatile
Ideal for 'spin-trim' and wheel-based productions lines.
Simple Training
1 day training for admin level users.
AVID Corporation is pleased to introduce the OVMS, an online vision measurement and monitoring system.
OVMS is designed to monitor the dimensional attributes of the thread finish area, measure those dimensions, and determine if those attributes meet set customer specifications. AVID has been a leading manufacturer of offline thread finish measurement systems (the AVBIS family) since 1992. AVID now applies this knowledge to online applications in the OVMS.
Many online system providers deliver modular vision solutions that are far too complicated for plant personnel to operate. AVID has observed that “all-encompassing” systems are difficult to maintain or adjust without vendor service. Additionally, the cost for a “basic” multi-region vision package is excessive for most packaging manufacturers, particularly those using EBM, IBM and small-cavity SBM processes.
The OVMS design principle was simple: build a system around a single region of interest, and build an easy-to-use interface that permits analysis of attributes within that region. The result is a system that is easy to deploy, easy to setup for new product, and easy to support.
The OVMS can also be configured as a single camera unit, monitoring a single angle of the bottle neck finish.
Measurement, Not Inspection
OVMS implements AVID’s proven lab measurement capabilities in this online monitoring platform. The standard two-camera package consists of two optical / illumination ‘rails’ that are positioned 45⁰ to the production line, 90⁰ to each other. This setup allows for 0/90 angle measurement of the bottle passing through the machine.
Unlike vision systems that require pattern recognition or templates, the system measures the actual bottle dimensions in real-time. While such competitive solutions are common, they frequently yield high reject rates due to the subjective nature of the actual defect.
All OVMS analysis is based on the measurement of attributes on the actual part passing through the system in real-time, and all pass/reject assessments are based on the numeric specifications entered by the customer. In this way, subjectivity is removed from the analysis, and verification can be accomplished using verifiable dimensional artifacts and tools.
OVMS can be configured as a simple pass/reject system based on the dimensional tolerances set by the system administrator. OVMS can also be setup to export bottle dimensional data to an output file in a number of ways: 100% data collection, timed interval data collection, sample set data collection, reject data only, or a combination. Reject is through a PLC generated signal for the user’s reject apparatus, which may also serve as reject confirmation.
Target application of the OVMS is the production line of bottles with stretch-blown or extrusion-blown neck finishes. The OVMS is a proven monitoring solution for PET blow-trim bottles and jars such as peanut butter and powdered food products. The OVMS is also appropriate and proven for HDPE/LDPE/PP bottle monitoring.